Організація виробництва (2003)
7.3. Визначення виробничого циклу складного процесу
Складний виробничий процес будується на великій кількості складальних, монтажних, регулювально-настроювальних операцій та операцій простих процесів, тому визначення й оптимізація виробничого циклу потребує багатьох варіантів розрахунків, що неможливо здійснити без спеціальних прикладних комп’ютерних програм та без застосування ЕОТ.
Побудова складного виробничого процесу в часі провадиться для того, щоб визначити виробничий цикл, скоординувати окремі прості процеси, отримати вихідну інформацію для оперативно-календарного планування виробництва i розрахунку операцій запуску-випуску предметів праці.
Метою координації виробничих процесів, що формують складний процес, є забезпечення комплектності i безперебійності виробництва при повному завантаженні устаткування, робочих місць та самих робітників.
Структура виробничого циклу складного процесу визначається складом операцій і зв’язками між ними. Склад операцій залежить від номенклатури деталей, складальних одиниць і технологічних процесів виготовлення та складання. Взаємний зв’язок операцій та процесів визначається схемою складання виробу і виробничими умовами. Складальна схема являє собою віяльну діаграму, на якій відображено комплектація окремих вузлів і виробів у цілому (рис. 7.3), а також які вузли, підвузли або дрібні складальні одиниці можна виготовляти паралельно незалежно один від одного, а які — тільки послідовно.
Особливість розрахунку виробничого циклу складних виробів полягає в тому, що вони запускаються на складання партіями. Партіонний метод забезпечує зростання продуктивності праці і зниження собівартості виготовлення продукції за рахунок: а) застосування найпродуктивнішого процесу; б) скорочення витрат ресурсів; в) зменшення підготовчо-завершального часу на одиницю продукції; г) швидкого опанування робітниками раціональних прийомів і методів складальних робіт; д) спрощення календарного планування виробництва.
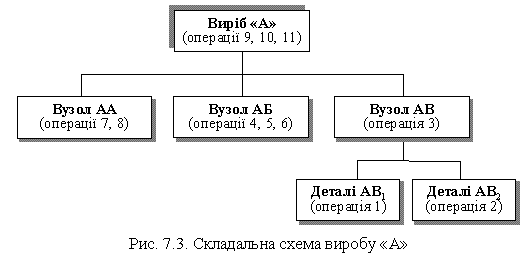
Для забезпечення точності розрахунку виробничого циклу використовуються календарно-планові нормативи: розмір партії; кількість партій, що запускаються; ритм. Використовуючи нормативні дані, послідовно визначають: час операційного циклу партій виробів за складальними одиницями; необхідну кількість робочих місць; цикловий графік складання виробів без урахування завантаження робочих місць; закріплення операцій за робочими місцями; стандарт-план складання виробу; уточнений цикловий графік з урахуванням завантаження робочих місць; тривалість виробничого циклу; випередження запуску-випуску за складальними одиницями.
В одиничному та серійному виробництвах важливо спочатку встановити економічно оптимальний розмір партії виробів, який є базовим для розрахунку інших нормативів. Відомо, що необмежене збільшення розміру партії порушує принцип безперервності, оскільки зростають, з одного боку, час пролежування кожної складальної одиниці і, відповідно, тривалість виготовлення партії, а з іншого — незавершене виробництво і додаткові площі для збереження цих складальних одиниць.
На практиці використовують спрощений метод розрахунку оптимального розміру партії. Для цього використовується відповідна таблиця.
Послідовність розрахунку така:
1. Установлення межі нормального розміру партії (nн) виробів
nmin nн nmax.
Для цього визначається розмір мінімальної партії, виходячи з затрат часу на переналагодження і поточний ремонт робочих місць (об). Для серійного виробництва об = 0,2 – 0,1 %, дрібносерійного і одиничного об = 2 – 10 %.
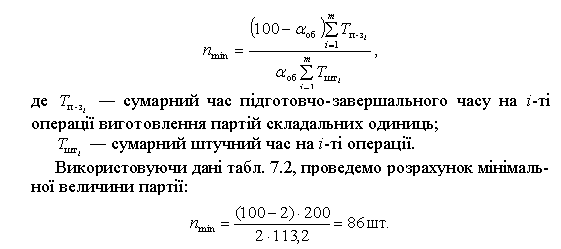
Місячна програма випуску виробів (складальних одиниць) зазвичай вважається як максимальна величина партії (у нашому прикладі пmах = 700 шт.). Коригування граничного розміру партії виробів здійснюється, виходячи з мінімального його значення. Спершу встановлюється зручний для планування ритм (Rпл) періоду черговості партій виробів за таких умов: якщо в місяці 20 робочих днів, ритмами будуть 20, 10, 5, 4, 2, 1; якщо 21 день, ритмами будуть 21, 7, 2, 1; якщо 22 дня, то відповідно — 22, 11, 2, 1.
Період чергування партій виробів розраховується за формулою:
Rпл = Др • пmin : пmах ,
де Др — кількість робочих днів у місяці.
Виходячи з наведеного прикладу, цей період дорівнюватиме:
Rпл = 21 • 86 : 700 = 2,58 дня.
У разі отримання нецілого числа вибирають із зручних для планування ритмів найближче ціле число, яке і буде прийнятим періодом чергування партій (Rпр). У даному випадку Rпр = 3 дні (з ритмів 21, 7, 3, 1).
Потім відповідно до прийнятого періоду чергування, коригуючи параметри, визначаємо розмір нормальної (оптимальної) партії за формулою:
nн = Rпр • пmах : Др = 3 • 700 / 21 = 100 шт.
Кількість партій у місяці (Х) визначається таким чином:
Х = пmах : пн = 700 : 100 = 7 партій.
Результати розрахунку оптимального розміру партії заносимо в гр. 6 табл. 7.2.
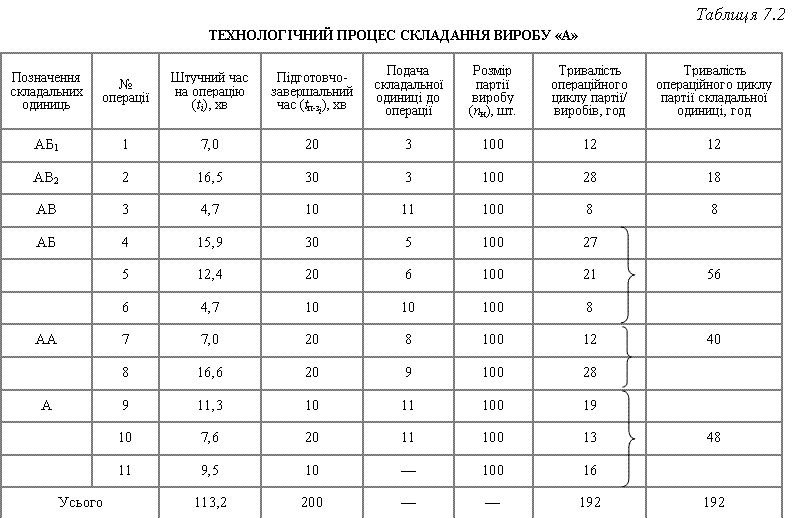
2. Тривалість операційного циклу партій виробів за кожною операцією (tin) розраховується за формулою:
tin = t • nн + Тп-зі : 60.
Для складальної одиниці АВ1
tin = 7 • 100 + 20 / 60 = 12 год.
Розрахунки записуються в гр. 7 табл. 7.2.
3. Тривалість операційного циклу партії виробів за складальними одиницями визначається за формулою:
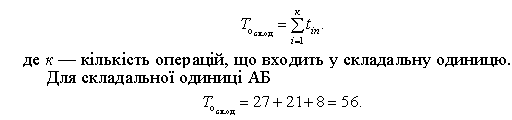
Аналогічно здійснюються розрахунки і за іншими складальними одиницями, результати яких записуються в гр. 8 табл. 7.4.
4. Необхідну кількість робочих місць для складання виробу розраховують так
РМпр = tі.шт / Тзм • S • Rпр.
У нашому прикладі РМпр = 192 / 8 • 2 • 3 = 4 робочих місця.
5. Кількість робітників визначається за формулою:
Чр.ск = РМпр • Кзм • Ксп,
де Кзм — коефіцієнт змінності;
Ксп — коефіцієнт, що враховує спискову чисельність (можна прийняти Ксп = 1,1).
Чр.ск = 4 • 2 • 1,1 = 9 осіб.
Побудова циклового графіка складання виробу «А» (рис. 7.4) здійснюється на основі складальної схеми (рис. 7.3), тривалості циклів виготовлення та складання кожної складальної одиниці (гр. 7, 8 табл. 7.2) без урахування завантаження робочих місць. Графік формується у зворотному порядку ходу технологічного процесу, враховуючи час завершення операцій, з яких здійснюється поставка оброблених деталей або складальних одиниць.
Наступним кроком є побудова стандарт-плану складання виробу «А», який має назву циклового графіка з урахуванням завантаження робочих місць. У стандарт-плані цикли окремих операцій проекціюються на відповідні робочі місця (рис. 7.4, б).
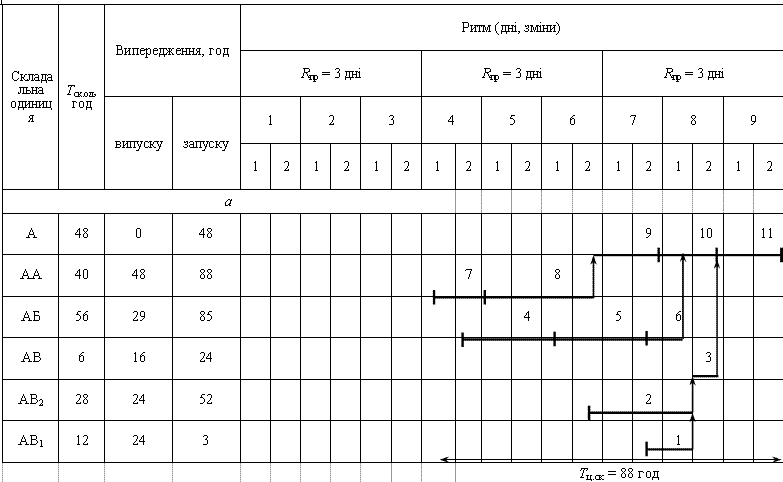
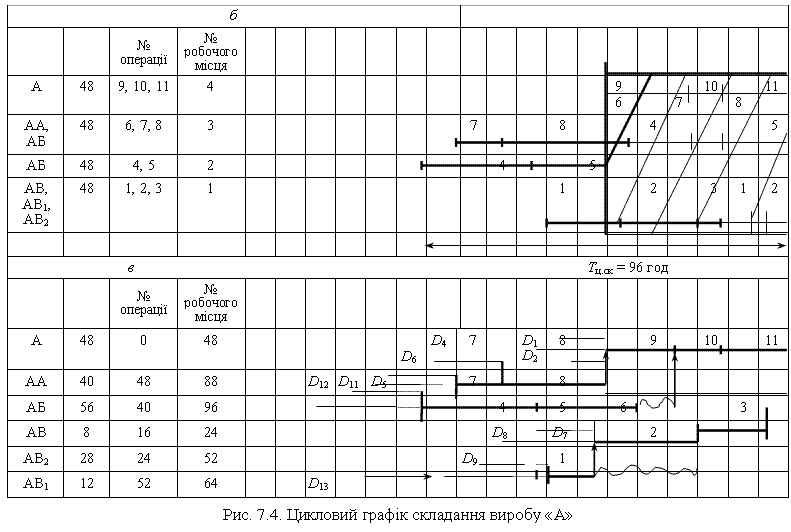
Принцип пропорційності полягає в рівномірному завантаженні робочих місць і робітників. Для його дотримання здійснюється розподіл обсягу робіт по робочих місцях таким чином, щоб тривалість операційного циклу кожної з них не перевищувала їх пропускну спроможність протягом прийнятого періоду чергування партій (табл. 7.3).
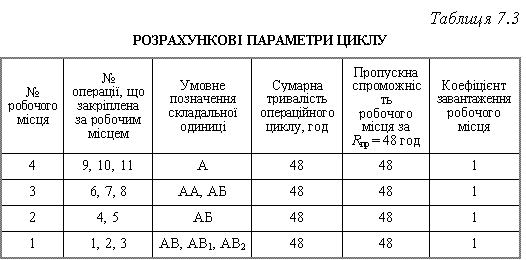
Зміщення початку виконання робіт зазвичай пов’язане з завантаженістю робочих місць. Так, зсув початку здійснення операцій 4, 5, 6, 1 (рис. 7.4, б) збільшив тривалість виробничого циклу, спричинивши пролежування складальних одиниць. Завдання полягає в організації виробництва другої, третьої та наступної партій виробів за термінами таким чином, щоб повністю заповнити період чергування цих партій. Після цього графік називатиметься стандарт-планом. У ньому показані стандартні повторювальні терміни проведення окремих операцій складання кожним робітником.
Побудова уточненого циклового графіка складання виробу (рис. 7.4, в) дає змогу визначити фактичну тривалість виробничого циклу, яка звичайно більша мінімальної тому, що виконання окремих операцій зсунуто на більш ранні терміни. Як показано на рис. 7.4, фактична тривалість виробничого циклу складання виробу збільшилася до 96 год. Хвильова лінія показує зміщення запуску відповідних складальних одиниць АБ та АВ1.
Для планування й організації виробництва важливим кален- дарно-плановим нормативом є випередження запуску-випуску складальних одиниць виробів. У нашому випадку його розрахунок здійснюється безпосередньо на самих графіках (рис. 7.4, а, в). Зсув запуску складальних одиниць АБ та АВ1 на раніші терміни (рис. 7.4, в) змінив випередження їх запуску-випуску. При цьому тривалість виробничого циклу стала на 8 год більшою, ніж на початковому графіку.
Для визначення повного виробничого циклу виготовлення готового виробу до циклового графіка складання додають графіки заготівельних та обробних процесів виготовлення деталей (рис. 7.5).
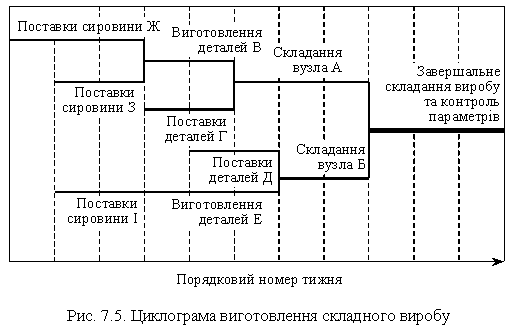
Виробничий цикл складного виробу дорівнює найтривалішому ланцюжку взаємопов’язаних робіт, що послідовно виконуються (тривалості виготовлення найбільш трудомісткої деталі з урахуванням партіонності, складання найбільш трудомісткого вузла і тривалості загального складання виробу).
Іншими словами, виробничий цикл складного виробу визначається найбільшою сумою циклів послідовно пов’язаних простих процесів і міжциклових перерв:
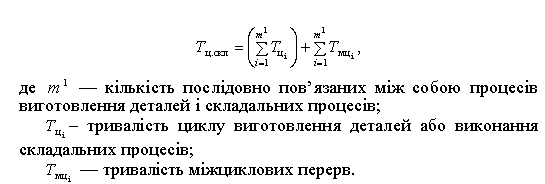
Цикловий графік дає можливість визначити термін запуску деталей у виробництво. При цьому запускаються деталі не всі одночасно, а виходячи з термінів подачі їх на складання й тривалості виробничого циклу та термінів випередження запуску порівняно з випуском.
При виготовленні складної продукції застосовуються сітьові методи планування, і тривалість виробничого циклу визначається довжиною критичного шляху.